The advantage of customising cement additives
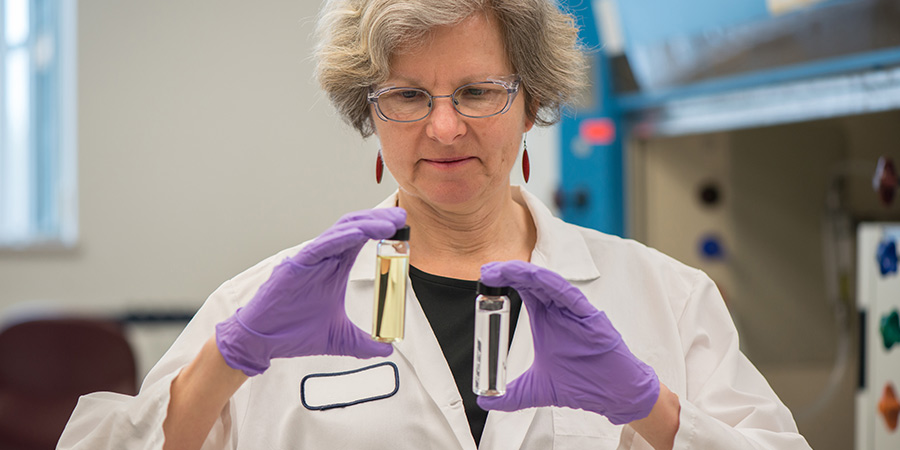
As most cement producers can attest, chemical additives are well established in the industry. However, customised additives have an edge over off-the-shelf solutions. The customisation of grinding additives enables cement producers to supply a product in line with its customers' needs. As such, they play a key role in helping improve cement quality, reduce production costs and improve a cement plant’s competitiveness in the market. One of the largest cement plants in western China recently worked with GCP Applied Technologies to develop a custom additive to improve its PO 42.5 cement.
Objectives
The Chinese cement plant produces several million tons of PO 42.5 cement per year. However, in the face of strong market competition, the firm began looking for ways to strengthen its market position with the use of quality improvers. The performance of the cement in its final application in concrete was identified as crucial to success.
After a preliminary screening of different chemical suppliers, the plant chose to partner with GCP Applied Technologies (formerly WR Grace) to not only help with the project but to help keep things evolving at the plant over time. A team of experts at GCP’s laboratory in Beijing works to develop customised cement additives. The team works closely with customers to understand their objectives and the constraints of the additive to identify a solution that meets all performance requirements at a minimal cost.
GCP assigned a dedicated team, including a sales engineer, a formulator and a concrete specialist, to work with the cement plant staff. Following a visit to the cement plant and a discussion with numerous of the plant’s ready-mix producer clients, the team identified the following objectives:
- Strength enhancement at all ages to allow 5% clinker replacement
- Improved particle size distribution
- Retardation of setting time by 30 minutes
- Constant water demand in paste (constant normal consistency)
- Improved slump retention up to 120 minutes
As part of the customisation, the team studied four supplementary cementitious materials (SCMs) and tested the effects of the SCMs and cement additives on:
- Compressive strengths (mortar and concrete)
- Particle size distribution (cement powder)
- Initial and final setting time (mortar)
- Normal consistency (paste)
- Calorimetry and sulphate balance optimisation (cement paste)
- Mortar flowability
- Concrete slump, slump retention and slump flow
SCM optimisation
After evaluating the cost, availability and performance characteristics of the SCMs, including granulated blast furnace slag, basalt, low siliceous sandstone and high siliceous sandstone, slag was selected as the primary means of clinker replacement.
Sulphate optimisation
To verify the optimum amount of SO3, 0.3 percent of SO3 was added in the form of a calcium sulphate hemihydrate to the blank cement, and the retention of mortar flowability was measured. The team observed improvement over the 120 minutes of analysis, suggesting the need for a slightly higher "gypsum" addition during cement manufacturing. Following plant verification, the additional SO3 level was implemented in the cement formulation.
Initial field trial
The team ran a field trial with GCP 215 quality improver, which met several targets including, strength enhancements at all ages, decrease in clinker from 79 to 74%, mortar flowability increase from 585 to 620mm at time 0 and improved particle size distribution. However, insufficient results were achieved for setting time and flow retention.
Advanced customisation
GCP then screened several new chemicals to find the ideal formulation to match GCP 215 with strength enhancement and a grinding aid, and to delay setting time and improve concrete rheology. The best candidate formulations were tested in concrete with a standard mix design, supported by reference materials shared by the cement plant. The test showed improvement in slump retention over the target period of two hours.
Second field trial
A second field trial was run with a modified version (GCP 31) of the best performing experimental additive, which confirmed the expectations (most notably, higher share of slag at same early strengths, longer setting times and improved concrete rheology).
Results of the second field trial with the GCP 31 additive
Cement sample | Clinker % |
Limestone % |
Slag % |
NC % |
IST (min) |
FST (min) |
3d (MPa) |
28D (MPa) |
Concrete slump at 0h (mm) |
Concrete slump at 2h (mm) |
Concrete spread at 0h (mm) |
Concrete spread at 2h (mm) |
---|---|---|---|---|---|---|---|---|---|---|---|---|
Blank | 78.5 | 8.0 | 7.5 | 26.4 | 198 | 257 | 28.3 | 56.0 | 235 | 220 | 535 | 450 |
GCP 31 | 75.5 | 8.0 | 10.5 | 26.6 | 221 | 288 | 28.9 | 56.5 | 235 | 220 | 570 | 555 |
Based on these results, GCP designed a tailor-made additive that enabled the cement plant to deliver a better and more competitive PO 42.5 cement to the market, with higher SCM content and improved concrete workability.
Tags
- Cement additives
- OPTEVA™