Improving particle size distribution in cement production
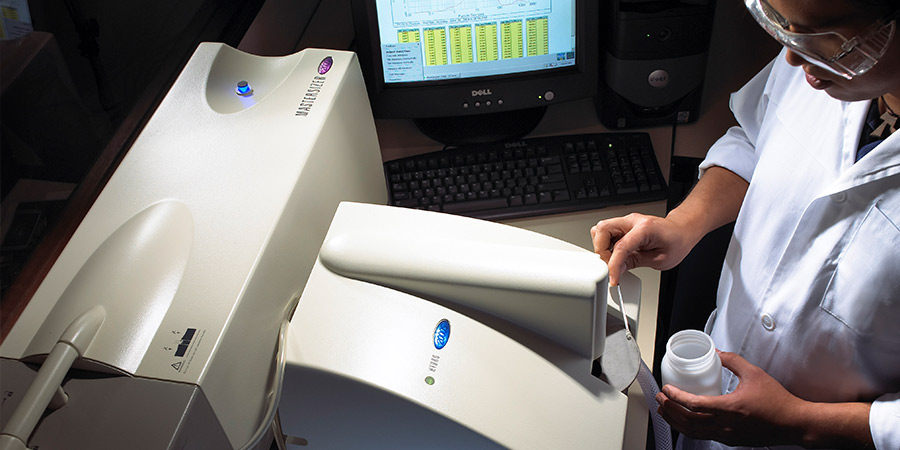
Enhancing cement grinding efficiency is beneficial for numerous reasons:
- Lower energy costs. An improvement in grinding efficiency means increased fineness at constant kWh/t or, more typically, lower kWh/t for constant fineness.
- Increased mill production. Higher grinding efficiency delivers the same fineness at higher output.
- Improved particle size distribution (psd). Grinding with higher efficiency means reducing coarse particles without over-grinding and producing super fines, hence a narrower psd is achieved.
- Improved strength. A narrower psd has less coarse particles, and a more complete hydration is possible, leading to greater strength.
Process improvements to circuit operation, separator design, mill internals or changes in mill type can result in higher efficiency of cement grinding.
Assessing cement fineness
In the past, cement producers gauged cement fineness (i.e., cement particle size) by evaluating the specific surface area (SSA) or Blaine fineness and the sieve residue at various sizes. However, many producers now use particle size analysis techniques to assess fineness and help monitor the efficiency of the mill. In the traditional Blaine SSA Fineness method, the fineness of cement is determined using an air permeability method in which dry air is passed at constant pressure through a compacted cylindrical bed of cement. To determine the SSA, the particle density is usually determined using a liquid displacement method or with a gas (e.g., helium) pycnometer.
Although the Blaine SSA is commonly used to describe the cement fineness, it doesn't always correlate well with actual cement properties, since the proportion of coarse particles (residue) can vary significantly for a constant SSA. Residues at sizes of 30-90 microns are routinely measured using a test sieve such as the Alpine air-jet sieve apparatus. To fully understand the influence of cement fineness on cement properties, producers need to more fully understand the complete psd.
There are a number of techniques for measuring psd. This includes laser diffraction (e.g., Cilas, Malvern, Sympatek) and sometimes sedimentation methods (e.g., optical or x-ray sedimentation). Based on these tests, the psd results can be described mathematically using the Rosin-Rammler equation.
Using fineness and residue as a guide to psd
When cement composition is constant, the residue and the SSA can be used as a guide to identify changes in psd. For example, the table below shows the estimated slope of the Rosin-Rammler psd from the SSA (in m2/kg) and the residue (at 45μm). The slope is based on the particle size data obtained by x-ray sedimentation.
Assessing mill efficiency
The slope of the Rosin-Rammler psd correlates well with mill efficiency, since higher mill circuit efficiency tends to produce a narrower psd. The table below provides a guide to the values of slope (n) for various grinding systems for CEM I type cements.
Mill System | Laser | Sedimentation |
BM - Open Circuit | 0.80 - 0.90 | 0.90 - 1.10 |
BM - Closed Circuit (1st Gen) | 0.90 - 1.10 | 1.05 - 1.15 |
BM - Closed Circuit (3rd Gen) | >1.10 | 1.20 -1.30 |
VRM | >1.10 | >1.20 |
Tags
- Cement production
- OPTEVA™